UV Curing System
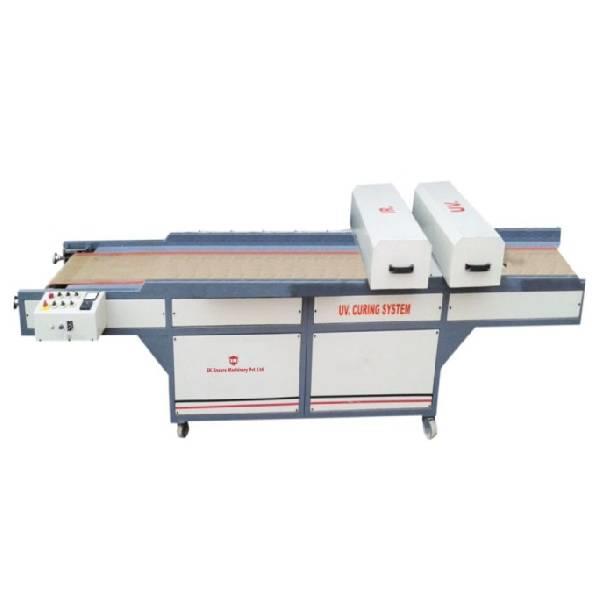
High intensity LED or UV spot-lamp light-curing systems quickly cure adhesives and coatings in under 10 seconds by delivering light energy to a very precise location. Systems can be used manually or in a high-speed automated assembly line. Ultraviolet curing (commonly known as UV curing) is a photo chemical process in which high-intensity ultraviolet light is used to instantly cure or “dry” inks, coatings or adhesives. UV formulations are liquid monomers and oligomers mixed with a small percent of photo initiators, and then exposed to UV energy.
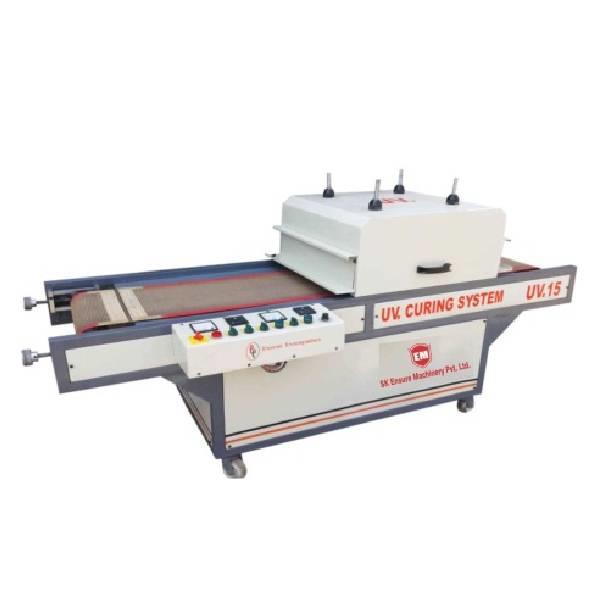
UV curing is used in applications where there is a need for converting or curing inks, adhesives, and coatings. UV-cured adhesive has become a high speed replacement for two-part adhesives, eliminating the need for solvent removal, ratio mixing, and potential life concern. Ultraviolet curing (commonly known as UV curing) is a photochemical process in which high-intensity ultraviolet light is used to instantly cure or “dry” inks, coatings or adhesives. UV formulations are liquid monomers and oligomers mixed with a small percent of photoinitiators, and then exposed to UV energy.
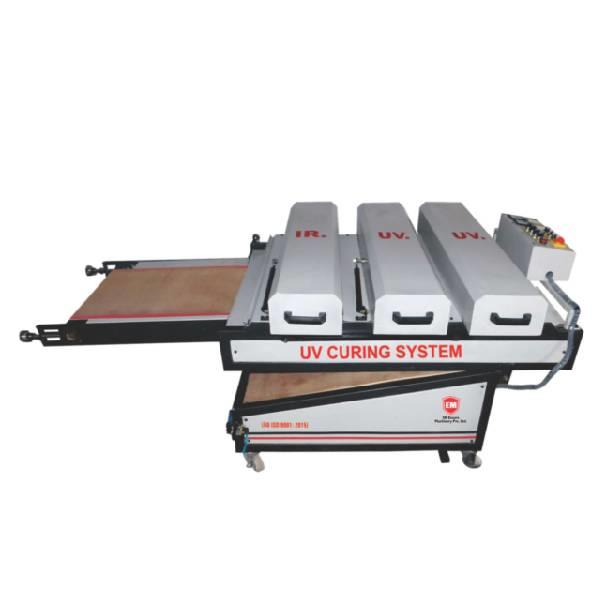
Ultraviolet curing (commonly known as UV curing) is a photo chemical process in which high-intensity ultraviolet light is used to instantly cure or “dry” inks, coatings or adhesives. UV formulations are liquid monomers and oligomers mixed with a small percent of photo initiators, and then exposed to UV energy. UV curing is used in applications where there is a need for converting or curing inks, adhesives, and coatings. UV-cured adhesive has become a high speed replacement for two-part adhesives, eliminating the need for solvent removal, ratio mixing, and potential life concern.
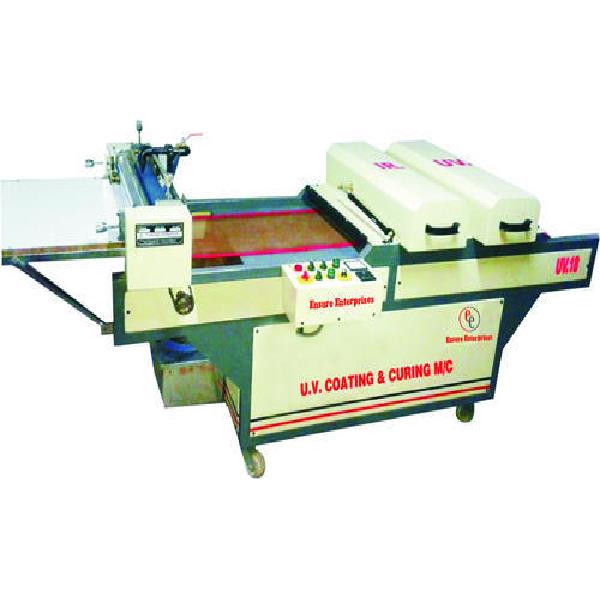
Offset UV Curing Attachments
₹
250,000.00
General Details: | |
model | Offset UV Curing Attachments |
Printing Technology | Uv Inkjet |
Voltage | 380V |
Frequency | 50/60 Hz |
Automation Grade | Automatic |
Usage/Application | Printing |
Others: | |
Application | Industrial |
Conventional offset printing uses traditional solvent-based inks that dry slowly by evaporation, giving them time to absorb into the paper. The absorption process is the reason colors can be less vibrant. Printers refer to this as dry back and is much more pronounced on uncoated stocks.Curing is the chemical reaction that takes place until the ink film has reached its maximum level of performance for adhesion, as well as for abrasion- and chemical-resistance. Most pad printing inks dry very rapidly and are “dry to touch” within a few minutes of printing.
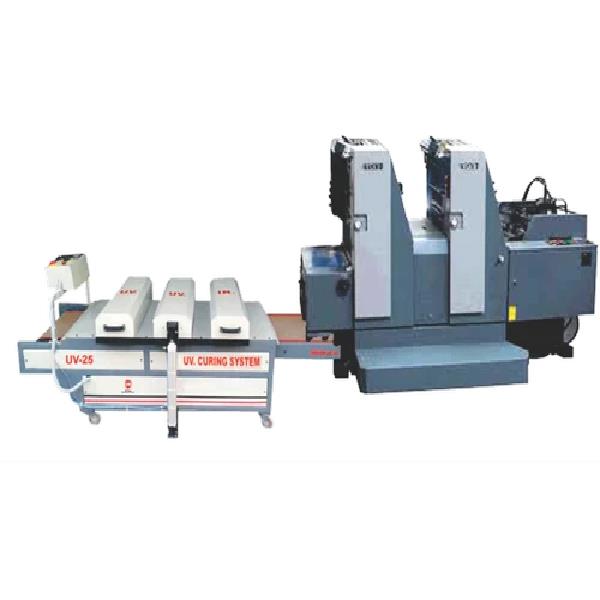
UV Interdeck Attachment
₹
150,000.00
General Details: | |
model | UV Interdeck Attachment |
Phase | Single and Three |
Usage/Application | For Offset Printing Machine |
Others: | |
Control Panel | Touch Screen |
Maximum Print Width | Customized |
Power Source | Electric |
Minimum Size | Customized |
It gives an extra advantage to the printer for printing with UV ink on Existing offset machine. With the help of this, PVC Laminated Board, Metalized, Laminated Paper & Board, Plastic sheets and various other materials can be printed. A high speed and a solid background Print can be done easily.

Offset UV Curing Attachment
₹
250,000.00
General Details: | |
model | Offset UV Curing Attachment |
Printing Technology | Inkjet |
Automation Grade | Automatic |
Usage/Application | Printing |
Others: | |
Model/Type | UV Curing |
Ink Type | Ink |
Ultraviolet curing (commonly known as UV curing) is a photochemical process in which high-intensity ultraviolet light is used to instantly cure or “dry” inks, coatings or adhesives. UV formulations are liquid monomers and oligomers mixed with a small percent of photoinitiators, and then exposed to UV energy.UV curing adhesives, also known as light curing adhesive, use UV light or other radiation sources to initiate the curing process. A permanent bond then forms without application of heat by a means of free-radical chemistry.
Tell us your Requirement
if you are interested, please fill the below details: